Evaluating Electrostatic Sprayers for Disinfectant Application
Watch the webinar recording on this research: COVID-19: Electrostatic Sprayers and Foggers for Disinfectant
Background
Recent research has shown that the COVID-19 disease is primarily caused by airborne transmission of the SARS-CoV-2 virus, but it is believed that the virus may also be transmitted via contact with contaminated surfaces (Pitol and Julian, 2021). Thus, routine cleaning and disinfection of potentially contaminated surfaces is recommended, among other infection control activities, to limit the spread of the disease. Business owners, school district leaders, and even mass transit leaders have needed to find ways to clean and disinfect large surface areas quickly and effectively that are frequently touched by many people. Thus, use of electrostatic sprayers (ESS) and foggers to rapidly apply disinfectants over large areas or complex, intricate surfaces has increased substantially with the COVID-19 outbreak. ESS have been used for many years in several other industries (e.g., efficient application of pesticides to crops), but recently they have grown in popularity as a technique to efficiently and rapidly apply disinfectants to surfaces, i.e., especially those that may be contaminated with the SARS-CoV-2 virus. These devices impart an electrostatic charge to the disinfectant spray droplets (most do so as the droplets exit the nozzle of the sprayer), with the goal of improving deposition of the droplets onto surfaces and thus promoting more efficient use of the disinfectant. This attribute may be both an advantage and disadvantage: an ESS may allow less disinfectant to be used to cover a surface area, but with less disinfectant applied, disinfection efficacy may diminish if the surface does not remain wet for the required contact time.
Challenge
There are several ESS parameters that may impact the disinfectant’s ability to inactivate the virus on surfaces, notwithstanding that an ESS is only as effective as the disinfectant chemical being sprayed (only EPA-approved disinfectants should be used for the SARS-CoV-2 virus and in accordance with the disinfectant product’s label).
These include the following:
- The amount of disinfectant to apply to a surface, i.e., the deposition rate (e.g., fluid ounces of disinfectant per 1000 ft2), so that the surface remains wet for the required contact time to ensure inactivation of the virus.
- The electrostatic charge imparted to the spray, potentially affecting its ability to deposit onto surfaces, including surfaces not in the direct path of the spray (e.g., the ability to wrap around and adhere to complex surfaces).
- The amount of the disinfectant’s active ingredient lost to the air before reaching the surface. Loss of the active ingredient to the air will diminish the concentration of the active ingredient on the surface, thus potentially reducing disinfection efficacy.
Other parameters may introduce exposure concerns by creating inhalation hazards to the operator of the ESS or those occupying the space following disinfection. These include the following:
- The droplet size distribution of the spray and chemical composition of the droplets. Smaller droplets are more readily inhaled and deposited deeper in the respiratory tract.
- The loss of the active ingredient of the disinfectant to the vapor phase during the spray process. Some disinfectant active-ingredient chemicals, such as chlorine and hydrogen peroxide, may volatilize and become hazardous if in sufficiently high vapor concentrations. This is a concern for the ESS operator, as well as for occupants of the space following disinfection (if not properly aerated).
Research Objective
The purpose of this research is to evaluate spray parameters for several different types of sprayers and foggers. Specifically, we are evaluating six ESS, two foggers, and one hand-pumped garden sprayer (Table 1). The hand-pumped sprayer is the only manual sprayer evaluated. Two of the ESS we are evaluating use alternating current (i.e., they are plugged in), while the rest rely on battery power. The sprayers were selected for our study based on an initial assessment of commercial availability.
Sprayers are used to apply disinfectant directly to a surface (recommended spray distances vary from about 2 feet to 10 feet), whereas foggers may be used for disinfection of surfaces or volumes (i.e., disinfection of air, inactivation of aerosolized viral particles). Because the disinfectant chemical fog can fill a room, they are usually operated automatically with no operator present. The two foggers we are evaluating do not use electrostatic charging of their droplets.
One ESS came with two different nozzles, stated to produce different size droplets, and thus both are being evaluated in our study. Another ESS has the ability to turn the electrostatic charge on and off; both settings are being evaluated.
Both water and disinfectants are being tested in the sprayers. Only disinfectants are being used in tests to evaluate loss of active ingredient, and in efficacy testing. Finally, we note that some of the sprayers were malfunctioning at the time certain parameters were being evaluated, and so not all sprayers were tested for every parameter.
Experimental Approach
This section briefly discusses the methods used to obtain data and information for the sprayer and fogger parameters presented in this data brief. The sprayer parameters evaluated and discussed in this brief include sprayer flow rate, recommended deposition rate, the droplet size distribution (DSD) of the spray, and the electrostatic charge of the spray. Note that other sprayer parameters will be evaluated as part of this study but presented in a future data release or in a final report.
Sprayer flow rate
Each sprayer’s flow rate was evaluated for 30 seconds by spraying into a large container and then transferring the liquid to a graduated cylinder for measurement. Sprayer flow rates were measured in conjunction with other tests, such as measuring the DSD or electrical charge tests (discussed below). The sprayer was running for a few seconds before placing the nozzle in the container and starting the timer. The sprayer output flow rates are presented in Table 1 in units of oz/min, and when considering the target deposition rate and surface area to be disinfected, provide an indication of the time required to dispense the disinfectant onto the surfaces to be disinfected.
Sprayer manufacturer-recommended surface coverage or deposition rate
This parameter is critical to ensure that sufficient disinfectant volume is applied to the surface such that it remains wet for the required contact time of the disinfectant, and thus ensures effective inactivation of the virus (and compliance with the EPA-required disinfectant label). This parameter was compiled from the sprayer user manuals, brochures, and distributer/manufacturer websites. Since ESSs are typically used for disinfection of large surface areas, the deposition rate is usually presented in units of fluid ounces of disinfectant per 1000 ft2. As previously discussed, foggers are primarily used for volumetric decontamination, and so no suggested surface coverage rate was provided for the two foggers we evaluated. This parameter is presented here to provide the user with an indication of the range in values as suggested by the manufacturers.
Droplet size distribution of the spray
The droplet size distribution (DSD) of a spray is typically characterized in terms of the volumetric median diameter (VMD), which refers to the droplet size in which half the volume of the spray is in droplets less than, and half of the volume of the spray is in droplets greater than, the VMD. It is typically reported in units of microns. Results for the DSD may also be reported in terms of other percentages for which the volume of the spray is less than the specified diameter. Examples include the Dv10 or Dv90, which is the droplet diameter in which 10% or 90% of the volume of the spray is less than that droplet size, respectively. These measurements provide additional characterization of the size range of the spray droplets than the VMD alone.
Data were collected for analysis of the volume-based size distributions using a forward scattering laser diffraction instrument (HELOS-KR Vario aerosol spray and particle analyzer); refer to Figure 1 for a photograph of the instrument in operation with an ESS. The instrument was placed in a recirculating wind tunnel and the tunnel was set to 20°C (±1°C) and 50% (±5%) relative humidity (RH). Each of the sprayers’ DSDs were measured at the bounds of the manufacturers’ recommended spray distances (where possible), as well as a third or fourth distance (within the bounds) for comparative analysis. Prior to each measurement, the wind tunnel fan was turned off so that there was no airflow. At each spray distance, the DSD was analyzed five times with the spray perpendicular to the laser.
The DSD of the sprayers was measured using deionized water as well as laboratory acquired tap water. For one of the ESS devices evaluated, the electrostatic charge function can be turned on and off, and so the DSD was measured for both settings. Another ESS came equipped with two different nozzle tips to adjust droplet size (a 40 micron and 80-micron VMD), and so the DSD was measured for both.
Following the tests with water, the DSD for one ESS was evaluated for three different water-based disinfectants to assess the impact the presence of the disinfectant solution might have on the DSD. The three disinfectants evaluated utilized an active ingredient of either chlorine, hydrogen peroxide, or quaternary ammonium. However, when testing the quat-based disinfectant, the spray penetrated the sheath air protecting the optics of the instrument and thus coated the lenses, rendering the data for this disinfectant unusable. The disinfectants were prepared according to the label directions.
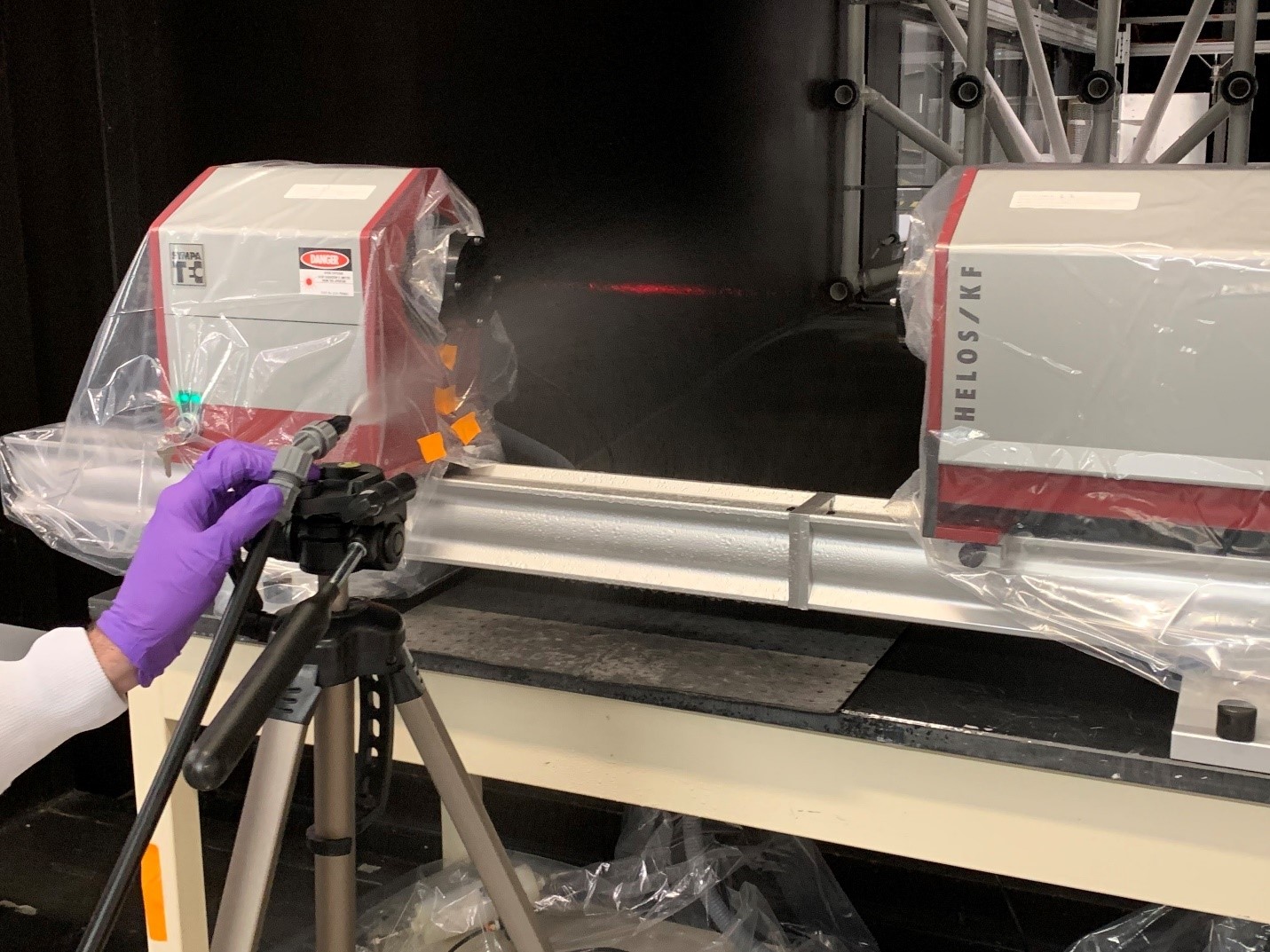
Electrostatic charge of the spray
The test apparatus used to measure spray charge consisted of an aluminum plate 20.1 in. by 11.4 in., mounted to plywood of similar dimensions using zinc screws at each corner. Two holes were bored at the top of the plate and rubber screen spline was used to suspend the plate 52 in. (to center point) from the floor in the center of the wind tunnel. The average wind tunnel temperature and RH measured approximately 23 °C and 47.0%, respectively. A Keithley 4145 picoammeter was used to directly measure current generated from spraying the plate with electrostatically charged droplets and was connected to the top corner of the plate via positive lead with an alligator clip. The other lead was sent to ground via a ground plug to wall receptable.
Each sprayer was sprayed directly at the plate from a one-foot distance, using a sweeping motion to fully wet the plate over the course of 30 seconds, while electrical current was measured. This process was repeated three times with the plate being wiped dry between each test. After three electrical current measurements were collected, each sprayer was evaluated for flow rate. The charge-mass ratio (Q/m) was determined by calculating the average current measured from the three tests divided by the mass flow rate. The liquid flow rate was converted to mass flow rate by multiplying by the density of water (1 g/mL). The charge to mass ratio results are reported in units of milliCoulombs/kg. All tests were conducted with the ESS operator wearing an insulator mitt, and all ESS were operated according to the manufacturers’ instructions provided, related to the use of any grounding requirements.
The electrostatic charge imparted to the droplets from the devices was measured for both tap water and deionized water, to determine if the presence of ions (which may alter the conductivity) had any effect on the spray charge. Charge measurements were conducted for all the devices, except for one of the foggers, which was not functioning during the time the tests took place. As with the DSD measurements, the spray charge was measured for both the “on” and “off” positions for one of the ESS, as well as for both nozzle tips for another ESS.
Following the tests using water, the spray charge for one of the ESS was evaluated for the same three disinfectants used in the DSD tests to assess the impact the presence of the disinfectant might have on the charge. Lastly, the electrostatic charge was evaluated as a function of spray distance (1, 4, 6, and 8 ft), using the Clorox 360 device with deionized water.
Spray deposition test
This series of tests was conducted to qualitatively assess, and document with photographs, the ability of the spray (electrostatic or not) or fog to wrap around and deposit on the sides and back of a cylindrical object. We began this series of tests using a metal trash can (11 inch height, 8 inch diameter; purchased with a black matte finish), and then followed with a few additional tests to examine the spray deposition on objects with more complicated surfaces, such as a step ladder, a clip-on lamp, and fold-out chair.
The spray devices were filled with an aqueous solution of fluorescent dye (Blue aqueous tracer, T-900, Black Light World, Cub Run, KY), at a dilution of 1:25 in tap water. (For the Clorox 360 sprayer, we used both tap and DI water as the diluent in these tests, to evaluate whether the lack of ions in the water affected deposition.) In each test, the spray nozzle was placed at the same height as the center of the can. Each sprayer was evaluated using three replicate trash cans (i.e., each can was sprayed separately). A 3-inch by 3-inch square was marked on each can at 90-degree intervals using a UV-A fluorescent pen, and labeled as front, back, left and right. Approximately 8 mL were dispensed in each spray test. During each spray, the sprayer was moved back and forth, so that the spray cone fully enveloped the can.
Following each spray, the lights in the test chamber were turned off, and two, 24-inch long black lights were placed in front of the can to observe the deposition of the fluorescent aqueous mixture. Digital photographs were then taken of the front quadrant of the can, and then the can was rotated in 90-degree increments and photographs were taken for each quadrant. Prior to spraying the trash cans, photographs were taken of each can as described above, to serve as controls. Following each sprayer evaluation, the three trash cans were washed with a laboratory-grade detergent, and then further cleaned using a mixture of isopropyl alcohol and acetic acid.
Loss of disinfectant active ingredient from spraying
In these tests, an ESS was used to spray two different disinfectants in a test chamber, with the air flow in the chamber shut off. Vapor phase measurements of the active ingredient were conducted during the spray process, i.e., we measured chlorine gas when spraying a dichlor-based disinfectant and hydrogen peroxide vapor when spraying the hydrogen peroxide-based disinfectant. We also measured the active ingredient concentrations in the liquid disinfectants at four point in the process: the disinfectant as prepared, after filling the sprayer reservoir, when collected directly from the spray nozzle, and when collected 3 feet away from the spray nozzle in 1-liter glass beakers. When collecting the disinfectant droplets in the glass beakers, the spray time was typically 1.5 minutes. Three replicate tests were conducted for each disinfectant. In all tests, the disinfectants were prepared with tap water as directed on the label.
Measurement of chlorine gas and hydrogen peroxide vapor were conducted in real time using electrochemical sensors (Analytical Technologies, Inc., Collegeville, PA). The sensor was suspended from the ceiling in the center of the test chamber, approximately 3 feet from sprayer nozzle.
The active ingredient concentration of the disinfectants was measured using wet chemistry titration techniques. Available chlorine (free as hypochlorite/hypochlorous acid and combined from dichlor) was measured when using the dichlor-based disinfectant, using a commercially available method (Hach high-range bleach test kit; Method 10100, model CN-HRDT; Loveland, CO) adapted from ASTM Method D2022-89. Titration with potassium permanganate was used for measuring the hydrogen peroxide concentration in the disinfectant solutions. Please refer to O’Brien et al. (1974) for more information on dichlor chemistry related to disinfection.
Wetness tests
This test series was conducted to determine whether test materials remain wet for 10 minutes after spraying with water, how much water is initially deposited, and how much is lost to evaporation (ten minutes is a typical contact time for many disinfectants). Five ESS configurations were evaluated by spraying water onto 14-inch by 14-inch coupons of either plastic, stainless steel, or glass. The coupons were oriented in both a horizontal and vertical position. Spray distances varied according to the sprayer, based on manufacturer recommendations, and coupons were sprayed until droplets started to visually coalesce on the surface. Temperature in the test chamber was controlled to approximately 21 °C and relative humidity was controlled to approximately 35%; air flow in the test chamber was approximately 1 m/s.
For each material/sprayer/orientation combination, one positive control coupon and three test coupons were used. For the positive controls, the coupon was sprayed and then immediately wiped dry with a laboratory tissue. The wipe was weighed before and after collecting the water from the positive control to determine the initial mass of water deposited onto the coupon. For the test coupons, a wipe was also used 10 minutes after spraying. The mass of water collected from the positive controls was then compared to the mass of water remaining after 10 minutes, to determine how much water had evaporated.
Current Results
The current results for spray parameters are summarized in Table 1.
Flow rate
A majority of the sprayers and foggers evaluated had flow rates in the range of approximately 3.7 to 6.1 fluid ounces per minute (oz/min). The hand pumped sprayer and one of the foggers had the highest flow rates, at 17 and 11 oz/min, respectively. The lowest flow rate observed was for the EM360 HH, at 1.9 oz/min.
Recommended surface coverage
The manufacturer recommended disinfectant surface coverage rates ranged from 2-53 ounces of disinfectant per 1000 ft2 for those ESS for which information was available. No surface coverage rates were recommended for the foggers, consistent with the approach that foggers are typically intended to be used as a volumetric (aerosol) decontamination device rather than strictly for application of disinfectant to surfaces. The manufacturer of the SC-ET ESS did not provide a surface coverage rate, but recommended that a wetness test be conducted to determine the proper coverage amount such that the surface remains wet for the required contact time. Note, that it is imperative that the surface remain wet for the required contact time as per disinfectant label requirements. The time the surface remains wet will depend on the initial surface coverage, as well as site specific conditions such as the disinfectant (e.g., its properties such as vapor pressure, temperature), the material type, and ambient conditions such as air temperature, relative humidity, and air flow across the surface.
Interim results from wetness tests (to be discussed in a later report) using water showed that in most cases materials remained wet for 10 minutes at typical deposition rates and ambient conditions.
Droplet size distributions of the sprays
For conciseness of data, Table 1 shows the range in average VMD values obtained for all sprayer configurations, distances, and sources of water tested. A majority of the devices evaluated had average VMDs ≥ 40 microns. Not surprisingly, the garden sprayer generally had larger droplets, with its maximum average VMD at 207 microns. The VMD of most of the sprayers generally decreased with spray distance, presumably due to the larger droplets falling out before reaching the optical path of the droplet size instrument.
The presence of an electrostatic charge had no significant effect on the VMD, as demonstrated with both sets of results for the PX200ES HH sprayer. The use of different nozzles to adjust the droplet size didn’t seem to have any effect on the VMD for the PX300ES backpack sprayer.
The test results also showed that the presence of ions in the water had no effect on the DSD (i.e., comparing deionized and tap water), and the use of disinfectants also had no effect on the DSD as well (see Figure 2 for example data).
We acknowledge that our testing only included one ESS to assess the effect of disinfectant chemistry on DSD, and that other sprayers’ DSDs may be impacted by these same disinfectants. In general, ESSs should be evaluated in conjunction with a specific disinfectant, i.e., the spray parameters should be evaluated as an ESS/disinfectant system.
Electrostatic charge
The electrostatic charge results are shown in the last column of Table 1. As expected, the fogger and hand-pumped sprayer showed no measurable electrostatic charge. Unexpectedly, one of the ESSs also showed no measured charge (360 Sterile R40). The two ESS that utilize alternating current (the SC-ET and the Clorox 360) demonstrated the highest charge (approximately -3.0 to -6.0 mC/kg), as well as having a negative charge. The sprays from the battery-powered ESSs all carried a positive electrostatic charge and were about an order of magnitude lower in charge compared to the SC-ET ESS.
It is not known what magnitude of charge is necessary to elicit benefits of electrostatic deposition of disinfectants on surfaces for virus disinfection. To put in perspective, it has been suggested that a charge of at least 0.1 mC/kg is needed to elicit electrostatic benefits (Gaunt and Hughes, 2004). Lastly, the electrostatic charge results were not affected by the presence of ions in the water, nor when spraying disinfectants, and were not affected by spray distance.
Measured Flow rate (oz/min) | Manufacturer Recommended surface coverage (ounces of disinfectant per 1000 ft2) | Volume median diameter range1 (microns) | Electrostatic charge (mC/kg)2 | |
---|---|---|---|---|
PX200ES HH (on)3 | 3.7 | 40 | 36-78 | 0.11 - 0.137 0.468 |
PX200ES HH (off)3 | 3.8 | NA | 38-86 | 0.004 – 0.005 |
PX300ES backpack; red (40 micron) nozzle4 | 3.9 | 28 | 38-61 | 0.049-0.053 |
PX300ES backpack; green (80 micron) nozzle4 | 4.5 | 28 | 32-55 | 0.045-0.049 |
SC-ET5 | 3.7 | Recommends wetness test to determine coverage | 25-28 | -3.28 to -3.56 |
Emist EM360 HH | 1.9 | 2 | 80-101 | 0.28-0.29 |
360 Sterile R40 | 6.1 | 53 | 42-71 | 0 |
Clorox Total 360 | 4.1 | 14 | 33-45 | -6.05 to -5.74 |
Garden sprayer Husqvarna | 17 | NA | 49-207 | 0 |
Airofog Flex ULV cold fogger | 4.4 | NA | 39-43 | 0 |
iPihsius KB-1500 12L | 11.2 | NA | 40-41 | Not tested6 |
Notes:
HH= handheld
- Range in average results based on tests done with DI and tap water, at 3-4 different distances.
- Range in average results using DI and tap water. Negative values indicate the polarity of the measurement.
- This model has ability to turn the electrostatics on and off.
- Backpack sprayer had different nozzles to adjust droplet size.
- Purchased in ~ 2015 and used in several studies over the years, prior to this study. All of the other devices evaluated were newly purchased for this study.
- This device was not tested for spray charge due to the sprayer becoming non-functioning after the DSD tests.
- Battery may not have been fully charged.
- Fully charged battery tested with tap water.

Spray deposition
Example photographs of the spray deposition results are presented here. These photographs are meant to provide a qualitative, visual understanding of the spray deposition and the “wrap around” effect, or lack thereof. A more complete dataset of deposition results will be presented in a final report.
Figure 3 is a composite image of four photographs taken of the 3-inch by 3-inch squares in each quadrant for one of the trash cans, prior to spraying the fluorescent dye solution. That is, these are considered blanks or controls, to indicate how the trash cans appeared under black light prior to spraying. As can be seen, all four sides of the can remain relatively obscure, as expected, without the presence of the fluorescent dye solution.

Figure 4 is a composite image like Figure 3, but with photo documentation taken after spraying the trash can. The front quadrant of the can shows the most deposition, as expected, with the tiny droplets being relatively visible. In viewing the right quadrant of the can, one can see illumination due to the spray deposition on the front of the can, with some of the spray deposition reaching to about one-third of the square. Results for the left side of the trash can are similar to the right side, i.e., a small amount of deposition occurred within the square, nearer to the front side. The back side of the cylindrical trash receptacle shows little if any deposition, indicating minimal “wrap-around” effect. Although when compared to the back side of the control trash can (Figure 3), the back side of the test trash can does not appear to be as obscure, indicating the possibility that some minimal amount of spray may have reached the back side.

Figure 5 is a composite image showing photos of the right side and underside of the small lamp, before and after spraying. The right side of the lamp appears to be well-illuminated after spraying, indicating good coverage and wrap-around, and tiny droplets can be seen. The portion of the right-side image near the back of the lamp (opposite of where it was sprayed) does appear somewhat darker, indicating less deposition. There appears to be more deposition on the side of the lamp compared to either side of the trash can, which may be due to the smaller diameter of the lamp. The underside of the lamp also seems to be well illuminated, indicating deposition, although individual droplets are not as visible as they are on the right side of the lamp.

Although not shown here, the qualitative deposition results were similar for all the sprayers and foggers evaluated when spraying the trash can, with some minor differences. As expected, the deposition was greatest at the front of the can, with some minor amounts of spray deposited on the sides (but with more deposited towards the front), and only minimal amounts deposited on the back of the can.
Loss of deposition active ingredient when spraying
The results for the tests to examine loss of the hydrogen peroxide active ingredient via the spray process are summarized in Table 2. As shown, there was no loss in the disinfectant concentration of hydrogen peroxide (after it was diluted per the label requirements) as measured from: the sprayer reservoir; when collected at the nozzle; and when sprayed and then collected 3 feet away. These levels were all 0.19 – 0.20 % hydrogen peroxide. The hydrogen peroxide concentration of the undiluted disinfectant, measured several months after it was obtained, was 6.0%, in contrast to the label indicating it to be 8%.
During the three spray tests, which took place over the course of 1.5 hours, the average vapor phase concentration of hydrogen peroxide was 0.2 ± 0.05 parts per million by volume (ppmv). The highest level of hydrogen peroxide observed in the vapor phase was 0.35 ppmv, which lasted approximately 10 seconds and is lower than the U.S. Occupational Safety and Health Administration Permissible Exposure Limit (8-hr time weighted average) of 1 ppmv.
Table 2. Fate of active ingredient concentration when spraying hydrogen peroxide-based disinfectant
Disinfectant sample location |
Hydrogen peroxide concentration (%) of disinfectant |
---|---|
Undiluted (as shown on label) |
8.0 |
Undiluted, measured approximately 5 months from purchase |
6.0 |
1:32 dilution (label directions for SARS-CoV-2) – collected from sprayer reservoir |
0.19 ± 0.0 |
Diluted per label – collected at nozzle |
0.19 ± 0.0 |
Diluted per label – collected 3 feet away |
0.20 ± 0.0 |
The results for the tests to examine the loss of free-available chlorine from the dichlor-based disinfectant via the spray process are summarized in Table 3. There was no loss in the disinfectant available chlorine level (free hypochlorite/hypochlorous acid and combined from dichlor) as measured from the sprayer reservoir, when collected at the nozzle, and when sprayed and then collected 3 feet away. These levels all ranged from approximately 4,400 – 5,000 ppm (parts per million by mass) free-available chlorine. However, in the first measurement of the sample collected 3 feet away, the free-available chlorine concentration was 1,703 ppm and is believed to be an erroneous result (although we are unsure of the source of the error). The free-available chlorine concentration of the prepared disinfectant (4,347 ppm) and as indicated on the label (4,306) were not significantly different from each other.
During the three spray tests, which took place over the course of 1.5 hours, the average chlorine gas concentration was 0.14 ± 0.02 ppmv. The highest level of chlorine gas was 0.19 ppmv, which lasted approximately 10 seconds. This concentration is lower than the National Institute of Occupational Safety and Health recommended exposure limit (15-minute average) for chlorine gas of 0.5 ppmv.
Table 3. Fate of active ingredient concentration when spraying dichlor-based disinfectant
Quantity |
Available chlorine concentration (ppm) of disinfectant# |
---|---|
As shown on label (4 tablets per quart) |
4,306 |
As prepared stock solution |
4,347 |
Sampled from reservoir |
4,607-5,028 |
Sampled from nozzle |
4,427-4,667 |
Collected 3 feet away |
1,703*-4,908 |
*The first reading for the 3 ft sample was 1703 ppm, which is believed to be an outlier since the other two samples were both > 4650 ppm
# Total concentration of free and combined chlorine from dichlor.
Wetness tests
The results for the wetness tests are summarized in Figure 6 and show the amount of water recovered from the test coupons initially after spraying (the positive controls) and after 10 minutes of drying time. The results are averaged across the five sprayer configurations tested, for the coupon orientation (horizontal or vertical) and material.
Although test materials were sprayed until droplets began to coalesce (a somewhat subjective determination), materials in the horizontal orientation generally had higher amounts of water initially deposited than when coupons were oriented vertically (presumably due to runoff). After the initial deposition results are converted to more typically reported units, average results for the vertical coupons ranged from 23-33 ounces per 1000 ft2, and average results for the horizontal coupons ranged from 38-65 ounces per 1000 ft2. The deposition results are generally consistent with manufacturer-recommended spray deposition quantities (see Table 1).
The percent water loss after 10 minutes for coupons in the vertical orientation ranged from 78-95%, while the loss of water for coupons in the horizontal position ranged from 65-81%. In both coupon orientations, the plastic material had the least amount of water loss. Out of a total of 90 test coupons, 12 were completely dry after the 10-minute contact time, and the majority of these were in the vertical position. Visual inspection of the coupons after 10 minutes showed that drying on the surface was uneven, such that portions of the surface were visibly dry, in contrast to the gravimetric method reporting remaining water mass for the whole area sampled. In other words, the gravimetric method we used may report remaining disinfectant for a particular surface area, although there may be significant portions of that sampled area that are visibly dry.

Disclaimer
EPA is conducting several studies to inform the response to the COVID-19 public health emergency. The summary here is intended to provide a simple representation of the results of on-going testing; therefore, only a brief description of the purpose of the study, methods, and interim results are provided. This study is being conducted in accordance with an approved Quality Assurance Project Plan. The interim results have been reviewed by internal EPA technical experts, quality assurance staff, and management. No interpretation of the interim results is provided. Once complete, the study and its results will be described in detail in a publication subjected to external, expert peer review. EPA does not endorse the purchase or sale of any commercial products or services.
Please visit the EPA webpage for more information on the research EPA is conducting in support of COVID-19 response capabilities.
Gaunt, L.F. and Hughes, J.F. (2004). Electrostatic charging of trigger actuated spray devices. In Conference Series-Institute of Physics (Vol. 178, pp. 59-64). Philadelphia; Institute of Physics; 1999.
O'Brien, J. E.; Morris, J. C.; Butler, J. N., Equilibria in Aqueous Solutions of Chlorinated Isocyanurate. In Chemistry of Water Supply, Treatment, and Distribution, Rubin, A. J., Ed. Ann Arbor Science Publishers, Inc.: Ann Arbor, MI, 1974; pp 333–358.
Pitol, A.K. and Julian, T.R. (2021) Community transmission of SARS-CoV‑2 by surfaces: risks and risk reduction strategies. Env. Sci. Technol. Lett., https://dx.doi.org/10.1021/acs.estlett.0c00966